Spot Welder
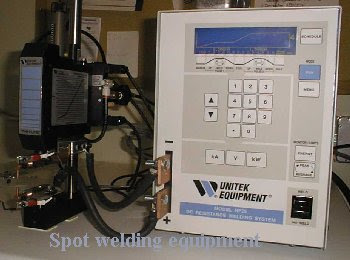
Resistance spot welding delivers an electric current to join materials through heating. The four stages in the welding process are squeeze, weld, hold, and release. During the first stage the materials are brought into contact through physical force. The welding current is then delivered and the materials are brought to their plastic state. By holding the materials together after the weld pulse the weld nugget solidifies and then the force can be released. The more control a welding instrument provides over each of these stages the greater the quality of weld that can be produced. Ideally, an instrument allows the operator to program weld cycles with specified currents and pressures.
When executing a typical single-pulse weld, the current travels through the points of initial contact at the junction. Due to the presence of the oxide layers at this interface the current will flow through the peaks created by the oxide layer forming a brittle weld between those peaks. In a dual pulse spot weld, a pre-pulse, prior to the weld pulse removes the oxide layer from the materials and increases surface contact to create an effective weld.
Variables that must be controlled by spot-welding instruments are energy, time, and physical force. The new High-Frequency Direct Current inverter (HFDC) systems provide highly programmable instruments that use feedback loops to accurately deliver the specifications of a welding cycle. Controlling the position of the welding tips and the physical force applied to the weld site, are necessary to achieve quality welds. Hand-held weld heads rely on operators' ability to choose, and maintain throughout the weld cycle, the position of the tips and the level of the force. Technological improvements such as air-actuated electrodes control the force with which materials are brought into contact, reduce operator variability and increase reproducibility of quality welds. The required force is set by the operator and the weld-head is driven by an air cylinder that maintains the preset force. Application of the required force as materials change volume during the weld cycle is central to the production of strong spot-welds. Another advantage of the air-actuated weld held is the decrease in crystal damage because the polished crystal face is not placed down face down during welding. The operator orients the crystal and other metal between the tips of the electrodes and uses the bi-level foot switch to apply force to the materials and then deliver the weld cycle.
When executing a typical single-pulse weld, the current travels through the points of initial contact at the junction. Due to the presence of the oxide layers at this interface the current will flow through the peaks created by the oxide layer forming a brittle weld between those peaks. In a dual pulse spot weld, a pre-pulse, prior to the weld pulse removes the oxide layer from the materials and increases surface contact to create an effective weld.
Variables that must be controlled by spot-welding instruments are energy, time, and physical force. The new High-Frequency Direct Current inverter (HFDC) systems provide highly programmable instruments that use feedback loops to accurately deliver the specifications of a welding cycle. Controlling the position of the welding tips and the physical force applied to the weld site, are necessary to achieve quality welds. Hand-held weld heads rely on operators' ability to choose, and maintain throughout the weld cycle, the position of the tips and the level of the force. Technological improvements such as air-actuated electrodes control the force with which materials are brought into contact, reduce operator variability and increase reproducibility of quality welds. The required force is set by the operator and the weld-head is driven by an air cylinder that maintains the preset force. Application of the required force as materials change volume during the weld cycle is central to the production of strong spot-welds. Another advantage of the air-actuated weld held is the decrease in crystal damage because the polished crystal face is not placed down face down during welding. The operator orients the crystal and other metal between the tips of the electrodes and uses the bi-level foot switch to apply force to the materials and then deliver the weld cycle.
Labels: Resistance Spot Welding, Spot Welders, Spot Welding
0 Comments:
Post a Comment
Subscribe to Post Comments [Atom]
<< Home