Friction Stir Welding Technology: Adopting NASA's Retractable Pin Tool

Friction Stir Welding, a process invented and patented by TWI, is a highly significant advancement in aluminum welding technology that can produce stronger, lighter, and more efficient welds than any previous process. Friction stir welding uses the high rotational speed of a tool and the resulting frictional heat created from contact to crush, stir together, and forge a bond between two metal alloys. A welding tool moves along the area to be joined while rotating at a high speed. The action between the tool and the aluminum creates frictional heat, which softens the aluminum but does not melt it. The plasticized material is then, in essence, consolidated to create one piece of metal where there were originally two. The weld is left in a fine-grained, hot worked condition with no entrapped oxides or gas porosity.
The majority of the process benefits stem from the fact that FSW is a solid-state process. Because there is no melting of the material, the majority of problems normally associated with conventional welding are eliminated including porosity, solidification cracking, and shrinkage. Since the shrinkage associated with the liquid/solid transformation is eliminated, distortion and residual stress are minimized. The process requires no filler material, so parent metal chemistry is maintained with no chemical segregation.
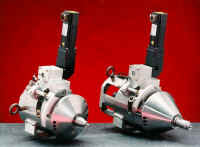
Although the technique is more reliable and maintains higher material properties than conventional welding methods, friction stir welding has had a major drawback of reliance on a single-piece pin tool. The pin is slowly plunged into the joint between two materials to be welded and rotated at high speed. At the end of the weld, the single-piece pin tool is retracted and leaves a keyhole, something which is unacceptable when welding cylindrical objects such as drums, pipes and storage tanks. Another drawback is the requirement for different-length pin tools when welding materials of varying thickness.

To overcome these drawbacks, a NASA Marshall Space Flight Center welding engineer helped design an automatic retractable pin tool that uses a computer-controlled motor to automatically retract the pin into the shoulder of the tool at the end of the weld preventing keyholes. This design allows the pin angle and length to be adjusted for changes in material thickness and results in a smooth hole closure at the end of the weld.
The possible application of FSW in construction area is as following:

The Benefits
The majority of the process benefits stem from the fact that FSW is a solid-state process. Because there is no melting of the material, the majority of problems normally associated with conventional welding are eliminated including porosity, solidification cracking, and shrinkage. Since the shrinkage associated with the liquid/solid transformation is eliminated, distortion and residual stress are minimized. The process requires no filler material, so parent metal chemistry is maintained with no chemical segregation.
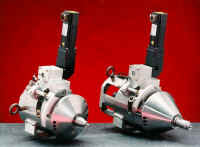
Although the technique is more reliable and maintains higher material properties than conventional welding methods, friction stir welding has had a major drawback of reliance on a single-piece pin tool. The pin is slowly plunged into the joint between two materials to be welded and rotated at high speed. At the end of the weld, the single-piece pin tool is retracted and leaves a keyhole, something which is unacceptable when welding cylindrical objects such as drums, pipes and storage tanks. Another drawback is the requirement for different-length pin tools when welding materials of varying thickness.

To overcome these drawbacks, a NASA Marshall Space Flight Center welding engineer helped design an automatic retractable pin tool that uses a computer-controlled motor to automatically retract the pin into the shoulder of the tool at the end of the weld preventing keyholes. This design allows the pin angle and length to be adjusted for changes in material thickness and results in a smooth hole closure at the end of the weld.
The possible application of FSW in construction area is as following:

- Construction Equipment (truck bodies, mobile cranes)
- Transportation including railroad industry (high speed trains, underground carriages)
- Bridge (aluminum components)
- Panels made from aluminum, copper or titanium
- Window frames
- Heat exchangers and air conditioners
- Pipe fabrication, etc.
The Benefits
- Diverse materials: Welds a wide range of alloys, including previously un-weldable (and possibly composite materials)
- Durable joints: Provides twice the fatigue resistance of fusion welds and no keyholes
- Versatile welds: Welds in all positions and creates straight or complex-shape welds
- Retained material properties: Minimizes material distortion
- Safe operation: Does not create hazards such as welding fumes, radiation, high voltage, liquid metals, or arcing
- No keyholes: Pin is retracted automatically at end of weld
- Tapered-thickness weld joints: Pin maintains full penetration
Labels: Friction Stir Welding, Welders
0 Comments:
Post a Comment
Subscribe to Post Comments [Atom]
<< Home